3d Printing Phoenix is an evolving manufacturing technique that regroups many different manufacturing methods: VAT photopolymerization, material jetting, SLS (Selective Laser Sintering), and SLA (Stereolithography).
Manufacturers use it for one-off productions of custom parts and devices to speed up prototyping cycles and facilitate innovation. Technology is also a great tool for creating replacement parts, reducing machinery downtime and increasing efficiency.
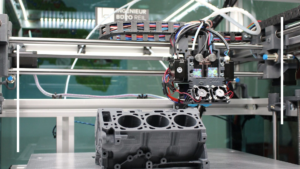
The rapid prototyping process is a valuable tool for new product development. It allows designers and engineers to create physical models of their designs for user testing and feedback. This allows them to make adjustments quickly and easily, saving time and money in the long run.
A rapid prototype is a scaled-down version of the final product made using an additive manufacturing process. Additive manufacturing uses a printer to construct three-dimensional objects by layering the raw materials, like paper or plastic, to produce complex shapes that would otherwise be difficult or impossible to create using traditional subtractive processes.
Unlike traditional manufacturing methods, such as machining or injection molding, which require costly tools and molds that can take weeks or months to build, 3D Printing is an additive process that eliminates the need for these expensive assets. With this flexibility, manufacturers can produce multiple copies of a part in a short amount of time, reducing costs and enabling them to test a larger range of geometries.
With a variety of material options, including PLA and ABS, 3D Printing offers the opportunity to use prototypes for functional testing, allowing them to be subjected to real-world conditions. It also enables a faster turnaround for iterative design, enabling teams to implement changes and improve performance before production begins.
In addition, a variety of metal 3D printing technologies are available that offer a high level of accuracy and strength compared to other traditional machining processes. Combined with optimized printing workflows and advanced features, such as PolyJet’s Air-As-Material technology, these advances help drive down cost and enable more sustainable design practices. Closed-loop recycling systems are also helping to reduce waste and minimize environmental impact.
Rapid Manufacturing
Using rapid manufacturing, businesses can produce scaled prototypes for testing and product evaluation. This is important because many companies, particularly those in industries such as medical technology and machinery, need to deliver top-notch products in a timely manner to meet customer demand. Traditional prototyping processes are expensive and take an extended amount of time to complete, which can be a significant hurdle for businesses that need to beat the competition to market.
Thankfully, 3d Printing and rapid manufacturing can help make this process easier, more affordable, and faster. The first step in the process is to create a digital model of the desired product through computer-aided design (CAD) software. This allows engineers to test the design and verify that it will function as intended before committing to expensive tooling.
Once the CAD model has been finalized, it can be converted into an STL file, which is the standard format for 3d Printing. This file represents the surface geometry of the model as a series of triangles, which the 3D printer can understand and replicate. Choosing the right material for the project is vital, as it must be capable of withstanding the stresses and strains that the prototype will be subjected to in its intended use.
Rapid manufacturing technologies can also reduce production costs by allowing for on-demand production and eliminating the need for extensive inventory. This can be particularly helpful for smaller projects, where the cost of a single prototype could otherwise be prohibitive. Another benefit of rapid manufacturing is reduced material waste, as only the required amount of material is used to make each part. This can reduce the need for costly disposal and recycling and improve overall environmental performance.
Customization
The idea of customization is a core part of 3d Printing. Unlike traditional manufacturing, which relies on standardized molds to churn out identical products in large volumes, 3d Printing uses digital models to create unique items. This allows companies to customize their product offerings and cater to specific customer needs.
With 3D Printing, manufacturers can adjust the dimensions, materials, and functionalities of their products to meet individual specifications with unprecedented precision. This allows them to differentiate themselves from the competition and provide customers with a customized experience that makes them feel more attached to their purchase.
While customization is a desirable feature for consumers, it can pose challenges for manufacturers. For example, designing a product for customization can require a redesign of its structure to ensure it is structurally sound and compatible with the selected material. It can also be challenging to optimize designs for printability and other mechanical properties, which may require collaboration between engineers and designers.
However, the benefits of customization can be worth the extra effort. For one, it can help businesses avoid the high costs of retooling and changeovers in production processes. It can also increase productivity and improve the quality of products in a short amount of time.
Additionally, consumers can leverage the power of 3d Printing to make their own custom products and accessories. For instance, eyeglasses and sunglasses manufacturers like Horizons Optical and Youmawo allow customers to design their own frames with the simple click of a button. The process involves a facial scan to collect biometric data, which is then used to create a unique pair of glasses that fits the customer’s face perfectly. The result is a truly one-of-a-kind pair of glasses that is sure to make a statement at any occasion.
Flexibility
Depending on the process used, 3D Printing can produce objects with a wide variety of characteristics. It is also flexible in terms of the materials it can print with, ranging from plastics to metals. It can also print in multiple colors. This flexibility is important for companies that want to create a variety of products and services to their customers.
A central element of most 3D printing processes is computer-aided design, or CAD. Using a three-dimensional model of the object to be built, engineers then translate this into a series of two-dimensional slices that are printed one on top of another in layers. The printer then solidifies each slice of material in a pattern according to the instructions generated by the CAD program.
This layer-by-layer fabrication approach to production makes 3D Printing more efficient than traditional manufacturing techniques. The technology eliminates the need to cast and mold parts or cut and machine them out of a block of material, which cuts labor costs and reduces the amount of waste created by the production process.
For example, car and aircraft manufacturers have embraced this technology, transforming unibody and fuselage design and powertrain production by using 3D-printed components. Boeing used 3D-printed titanium in its 787 Dreamliner airplane, for instance.
Doctors and medical technicians are also using the technology to produce prosthetics, hearing aids, artificial teeth and bone grafts, and replicating models of tumors and organs from CT scans in preparation for surgery. This is a powerful new tool for healthcare, and one that has the potential to significantly reduce the cost of procedures while improving patient outcomes.
Sustainability
The ability to produce products in-house reduces lead times and dependence on third party suppliers, allowing businesses to respond quickly to changes in demand or design iterations. It also minimizes product waste through a design for manufacturing approach that only produces the exact quantity required. This eliminates the need for a huge inventory of stock which is often discarded or becomes deadstock, as well as reducing energy and shipping costs.
Moreover, 3D Printing can be used to create spare parts for existing products and components, which promotes circularity. These printed components can be repurposed to repair other components in the system or replace worn parts, thereby significantly extending the lifespan of the products.
Another sustainable feature of 3D Printing is the ability to use recycled materials, reducing the need for virgin materials. This also helps to conserve natural resources and prevents waste from landfills. The technology also uses a fraction of the energy needed to operate traditional equipment and transport materials, further reducing its environmental impact.
It is important to note that although 3D Printing offers many environmental benefits, it is not without its limitations. Some concerns include the need for water usage, emissions from printing material, and the energy required to heat and operate the printers. Some prints may also emit volatile organic compounds (VOCs), which can cause air pollution and harm human health.
However, these issues can be addressed with proper education and research into sustainable practices. As the technology continues to evolve, it is expected that it will continue to be a viable option for manufacturing, as well as an excellent tool in creating more sustainable buildings and infrastructures. In fact, a bridge was recently built in the Netherlands using 3D Printing, showcasing the potential of this innovative technology.